Knowledge of data transfer from manufacturing processes
The first and most crucial factor for the data analysis is to define the purpose of collecting process data. You should know quality issues in processes and clearly understand why you collect data, what data you need, and how much or how often you need to collect data. Data collection without explicit purposes is not worth anything.
Second, many manufacturing facilities are used in processes. Some facilities export data with process names, product numbers, feature names, and serial numbers, while a simple gauge outputs measured data only. You might not have all the information required for data management in the data file. You might not even get digital data sometime. You must consider how you supplement missing information before starting data collection.
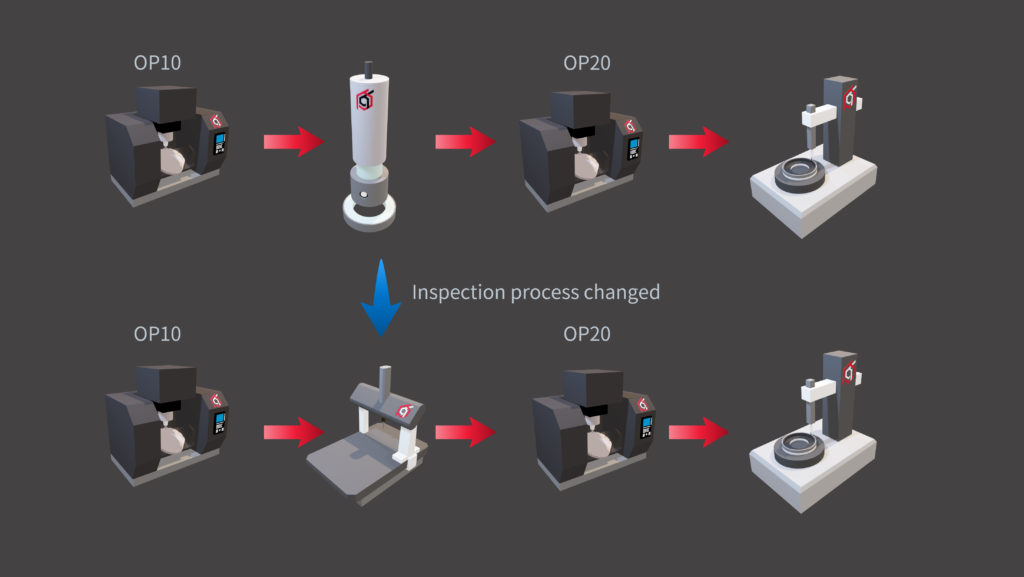
Third, you might need to stop the data collection from a device for periodic maintenance while others are still working. You might need to stop collecting data from a specific part or characteristic because they are obsolete. After starting automatic data collection, you will notice that you need to change the data collection settings more than you expected. Automatic data collection does not mean you don't need to do anything. If a production or an inspection changes, the data collection must change accordingly. Otherwise, the data will be unable to keep up with processes.
The IT department usually sets up the data collection system, but only data users can foresee these issues.
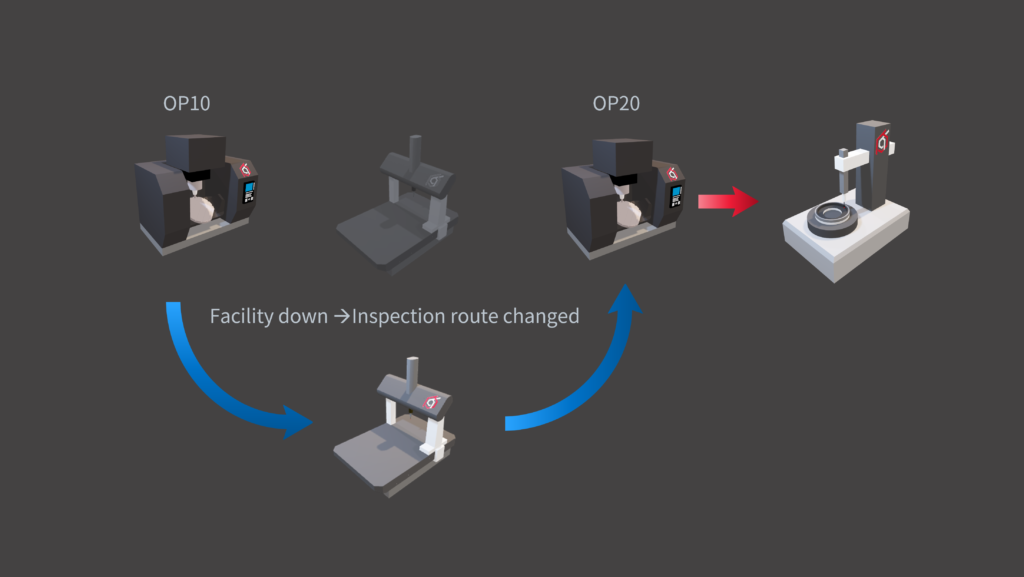